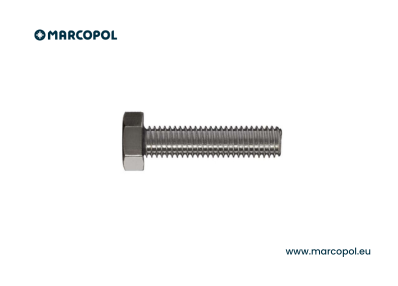
A deep dive into screw classes
In every corner of the construction and mechanical world, screws play a pivotal role far exceeding their diminutive stature. These fundamental components are paramount in maintaining the integrity and precision of various structures and machines.
The diversity found in their forms and sizes is matched by the critical distinctions in their strength ratings, making them indispensable in a wide array of applications. A deeper understanding of screw strength classifications is not just for industrial experts and professionals; it’s valuable knowledge for DIY enthusiasts and engineers alike.
The essence of screw strength ratings
Central to the selection of screws is the concept of strength classification. This criterion does not concern itself with the screw’s dimensions but focuses on the tensile strength of the material from which the screw is crafted. Tensile strength is defined as the maximum stress a material can withstand while being stretched or pulled before it breaks.
Unraveling the code. The two-digit strength rating
The strength of screws is often represented by a two-digit numeral, with each digit playing a crucial role in highlighting the screw’s performance:
- The initial digit signifies the material’s minimum tensile strength (Rm) divided by 100. This number reflects the maximum stress (in N/mm²) the screw can withstand before it experiences plastic deformation and ultimately fails.
- The subsequent digit denotes a ratio of the yield strength (Re) or the conventional yield point (R0.2) to the tensile strength (Rm), all divided by 10. This ratio indicates the stress threshold beyond which the screw will begin to deform permanently.
For example, according to the Polish Standard PN-M-82084, screws are classified into ten primary strength categories, from 3.6 up to 12.9. The numerically higher classifications indicate screws made from sterner stuff, which, while stronger, tend to be less ductile and more prone to brittleness.
Letters in the mix: The alphabetical classifications
Beyond the numeric system, screws can also bear letter grades from A through C, each marking:
- A — Precision
- B — Moderate precision
- C — Basic
Additionally, a special designation, the H class (like 14H, 22H, 33H, 45H), is tied to 10% of the material’s Vickers hardness (HV), a gauge of how resistant the material is to being indented.
The real-world relevance
Selecting the appropriate screw class goes beyond ensuring a snug fit; it’s about securing the durability, functionality, and safety of whatever is being assembled. While the specifics might be overlooked for trivial home fixes, the choice of screw class becomes crucial in industrial applications where the consequences of failure are much more severe. The right screw does more than just join two pieces; it carries the burden of daily operations, warding off deterioration, damage, and breakdown.
To wrap up, the realm of screws is extensive and multifaceted. Whether you’re replenishing your home workshop or detailing materials for an expansive construction project, grasping the basics of screw classes can help ensure your endeavors are built to last and perform. For patrons of Marcopol, this insight guarantees that selecting screws is a deliberate process, culminating in constructions that are robust, dependable, and secure.