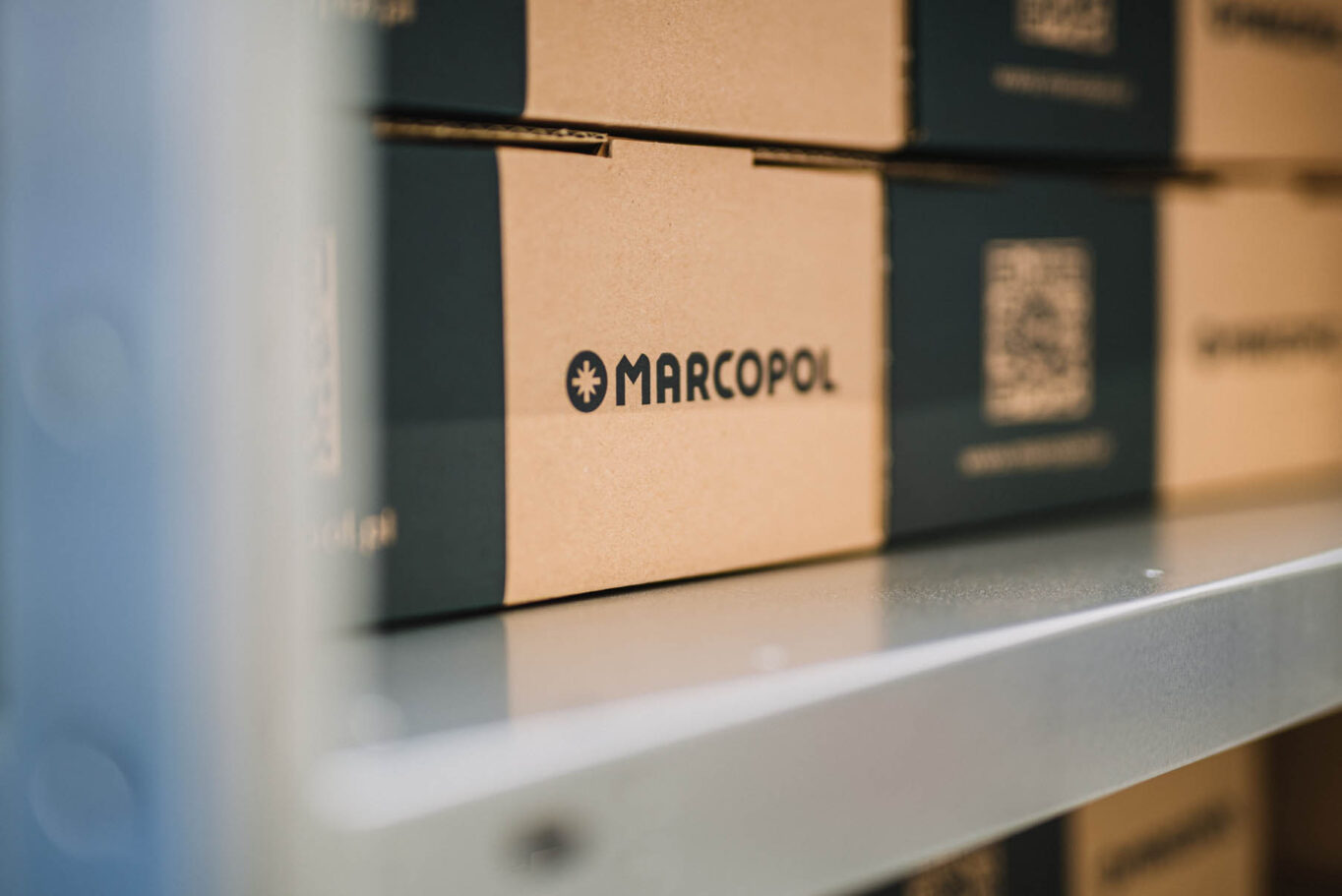
Comparison of different fastener quality standards – what you need to know?
Fasteners, such as screws, nuts, washers, or bolts, are essential components in construction and assembly that determine the durability and reliability of connections. However, their quality and technical parameters vary depending on the accepted standards.
The most commonly encountered standards are ISO, DIN, and ASTM – each with specific requirements that are worth understanding to make an informed choice.
ISO, DIN, and ASTM Standards – what are the differences?
- ISO (International Organization for Standardization) – This is a global standard that defines the technical requirements and dimensions of fasteners. ISO standards are widely used worldwide, making them universal and recognizable across many industries. Fasteners meeting ISO standards are characterized by dimensional and strength standardization, making them easier to use in international projects.
- DIN (Deutsches Institut für Normung) – This is the German standard, which until recently was one of the most commonly used in Europe, especially in German-speaking countries. Although many DIN standards have been harmonized with ISO standards, there are still significant differences, particularly with older standards. Products marked with DIN are often preferred in industries where precise German engineering is key.
- ASTM (American Society for Testing and Materials) – These are standards developed mainly for the U.S. market, focusing on strength testing and material quality. ASTM standards precisely define how to test the mechanical properties of fasteners, which is particularly important in heavy industry and construction.
What does these standards mean for the final user?
From the perspective of the end user, the choice of fasteners compliant with specific standards directly impacts the durability, safety, and reliability of connections. Here are a few key aspects to consider:
- Material Durability – Standards specify the minimum requirements for tensile, shear, or fatigue strength of materials. For example, products compliant with ASTM standards are often tested under higher loads, making them particularly useful in challenging working conditions.
- Precision of Manufacture – Fasteners compliant with ISO and DIN standards are usually characterized by greater manufacturing precision in terms of dimensions, which is crucial in applications where tight tolerances are necessary.
- International Compatibility – ISO standards ensure global compatibility, which is important when products are used in international projects. For example, purchasing screws in Europe ensures they will fit devices produced in Asia or North America.
- Cost and Availability – Fasteners compliant with ISO standards are usually widely available and often cheaper compared to those compliant with ASTM standards, which may require more advanced quality testing.
Standards and the actual durability and reliability of connections
The choice of standard impacts the performance of fasteners in practice. For example, for connections exposed to extreme environmental conditions, such as high temperatures or moisture, ASTM standards may provide greater reliability due to stringent testing for corrosion resistance and other factors. On the other hand, in applications where precision and repeatability are crucial, DIN or ISO standards might be a better choice due to strict dimensional tolerances.
Understanding the differences between ISO, DIN, and ASTM standards is crucial to selecting the right fasteners for a particular project. These standards differ in terms of technical, strength, and manufacturing precision requirements, which directly affects the quality of connections, and therefore the safety and durability of the entire construction. Depending on the specifics of the project, the end user should consider both the technical requirements and the availability of fasteners compliant with the given standards. Choosing the right standard is an investment in the durability and reliability of connections.