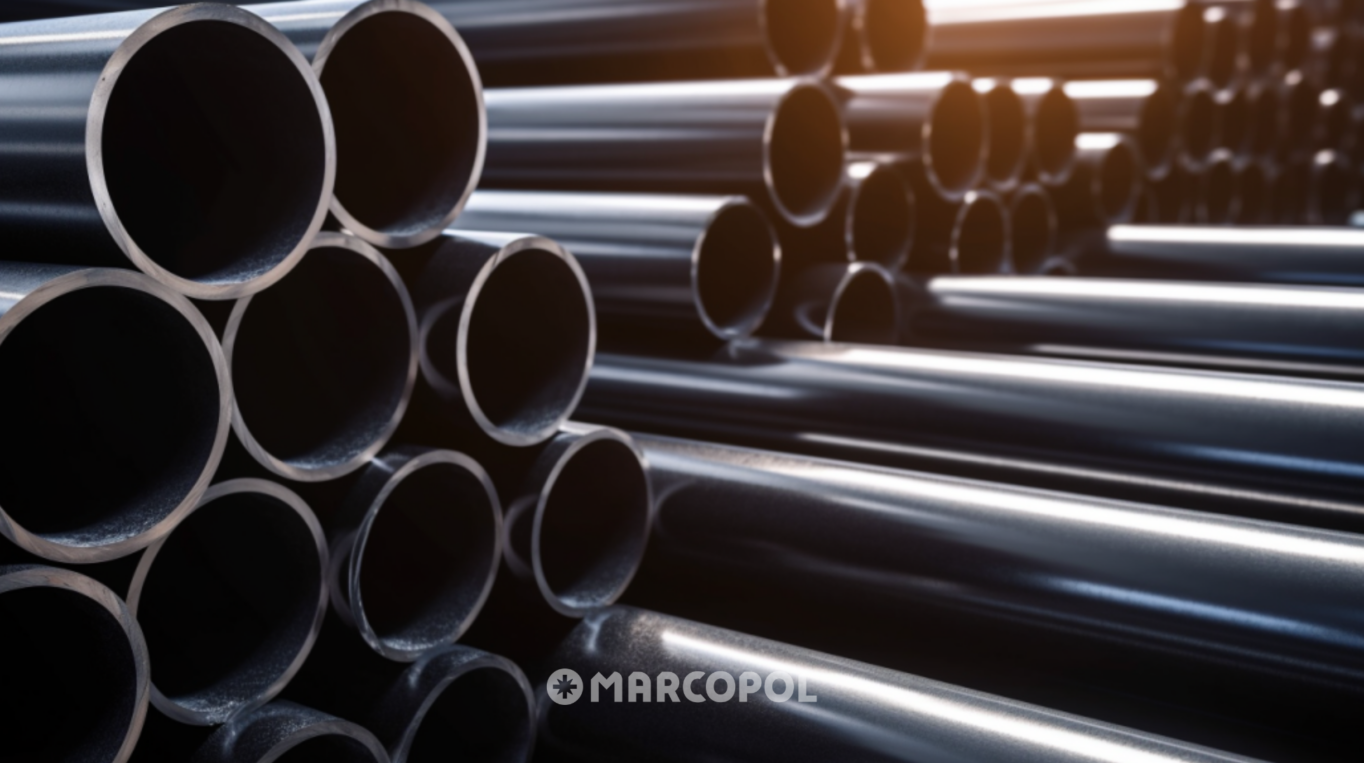
Key differences between stainless steels A2 (AISI 304) and A4 (AISI 316)
Stainless steel is a widely used material in various industries, with A2 (AISI 304) and A4 (AISI 316) being the two most commonly utilized grades. While both materials are characterized by excellent corrosion resistance, they differ in chemical composition and properties, which influence their applications in different environments. Below, we present the key differences between these two types of stainless steel.
Chemical Composition
A2 Steel (AISI 304)
A2 stainless steel primarily consists of 18–20% chromium and 8–10.5% nickel. The absence of molybdenum in its composition limits its resistance to corrosion in highly aggressive environments, such as marine or chemical industries. However, it is an excellent material for use in moderate atmospheric conditions and standard indoor environments.
A4 Steel (AISI 316)
Compared to A2, A4 steel contains a similar chromium content (16–18%) and a higher amount of nickel (10–14%), along with 2–3% molybdenum. The presence of molybdenum significantly enhances its corrosion resistance, especially in chloride-containing environments such as seawater.
Corrosion Resistance
A2 Steel
A2 steel provides good corrosion resistance in typical atmospheric conditions and moderately aggressive chemical environments. It is widely used in indoor applications and in situations where exposure to extreme external factors is minimal.
A4 Steel
Thanks to its molybdenum content, A4 steel offers superior corrosion resistance, particularly in environments exposed to salt, acids, and other aggressive chemicals. It is an ideal choice for marine, chemical, and other industries where high resistance to corrosive agents is critical.
Mechanical Strength
Both A2 and A4 grades are characterized by high mechanical strength and resistance to damage. However, A4 steel exhibits slightly better tensile strength and higher resistance to elevated temperatures, making it more suitable for demanding industrial applications.
Cost
A2 Steel
Generally, A2 steel is a more affordable option than A4 steel, making it a cost-effective choice for standard operating conditions.
A4 Steel
Due to its more advanced chemical composition and higher corrosion resistance, A4 steel is more expensive. However, the higher cost is justified in applications where durability and resistance to external factors are a priority.
Applications
A2 Steel
A2 steel is commonly used in construction, food, and medical industries. It is suitable for environments that are not highly aggressive, such as indoor installations and decorative elements.
A4 Steel
Thanks to its enhanced corrosion resistance, A4 steel is frequently chosen for applications in the marine and chemical industries, as well as in environments exposed to aggressive chemicals, such as swimming pools, chemical plants, and shipyards.
The choice between A2 and A4 stainless steel depends on the specific project requirements and the conditions in which the materials will be used. A2 steel is a more economical option for standard applications, whereas A4 steel, with its superior corrosion resistance, is ideal for aggressive and demanding environments. Understanding these differences ensures optimal material selection, leading to greater durability and reliability of the final products.
By ensuring proper connections and selecting the right materials, Marcopol guarantees the highest quality and longevity of fasteners, regardless of the conditions in which they are used.