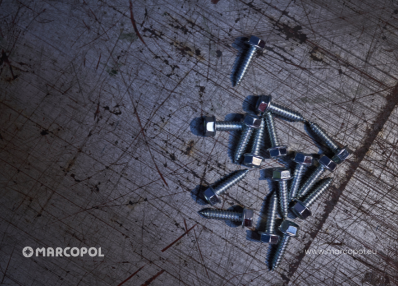
Types of screws. Class, markings, standards, and strength
Screws are key components in many mechanical structures, and their diversity can be astonishing. In this article, we will discuss the basic types of screws, their markings, strength classes, and the standards that are important in various applications. Understanding these aspects is essential for anyone working with fasteners.
What are the basic types of screws?
Among the basic types of screws, we distinguish hex head screws, cylindrical head screws, button head screws, and conical head screws. Each of these types has its unique applications and characteristics. For example, hex head screws are commonly used in construction and mechanics where high strength is required. On the other hand, screws with threads along the entire shank are often used in connections requiring stability and resistance to tension.
It is also worth noting the division of screws based on the type of thread, which can be metric or imperial. Metric thread screws are most commonly found in Europe, while imperial threads are popular in the United States. The diversity of screw types allows for their versatile use in various fields, from industry to craftsmanship.
How to read screw and nut markings?
The markings on screws and nuts are crucial for identifying their properties and applications. They usually consist of several elements, such as the strength class and thread type. For example, the marking 8.8 refers to steel with a tensile strength of 800 MPa and a yield strength of 640 MPa. It is important to be able to read these markings to select the appropriate screw for a given application.
In the case of nuts, the markings also include information about the strength class and thread type, which is essential for ensuring compatibility with screws. It is worth noting that in engineering practice, knowledge of these markings allows for precise selection of components, which is crucial for the safety and durability of structures. Therefore, every engineer or technician should know how to read these markings.
What are the strength classes of screws?
The strength classes of screws define their mechanical properties, such as hardness, plasticity, and tensile strength. The most commonly used classes are 5.8, 8.8, 10.9, and 12.9. Class 5.8 means that the screw has a yield strength of 400 MPa, while class 12.9 is characterized by a strength of 1200 MPa. Such markings are essential in applications where high load resistance is required.
In engineering, strength classes are often used to determine the loads a screw can withstand, which is crucial in structural design. Proper selection of the strength class is important not only for performance but also for the safety of the entire structure. Remember that an inappropriate choice of class can lead to failure, which can have catastrophic consequences.
What are the differences between standard screws and special screws?
The differences between standard screws and special screws lie mainly in their application and the materials from which they are made. Standard screws, such as hex head screws, are commonly used in many standard applications. On the other hand, special screws, such as screws with threads on part of the shank, are designed with specific technical requirements in mind. They may have unique shapes or properties that are necessary in certain industries.
Additionally, special screws can be made from more advanced materials that provide better strength or corrosion resistance. For example, the aerospace industry often uses titanium screws, which are lighter and stronger than steel ones. Understanding the differences between these types of screws is crucial for engineers and designers to select the appropriate components for their projects and ensure their reliability and safety during operation.
What are the characteristics of steel and stainless steel screws?
Steel screws are widely used due to their high strength and hardness. Their mechanical properties often depend on the type of steel they are made from. For example, steel screws can have different strength classes, including 8.8 and 10.9, making them ideal for applications requiring heavy loads. However, it is important to remember that steel is not corrosion-resistant, which is a significant factor for structures exposed to weather conditions. Therefore, they are usually coated with protective layers, such as zinc.
On the other hand, stainless steel screws, made from corrosion-resistant materials, are often used in environments where moisture or aggressive chemicals are present. Their strength can be comparable to steel classes, but their main advantage is resistance to rusting. Stainless steel screws are ideal for applications in construction, the food industry, and medicine. It is important to select the appropriate type of screw depending on the usage conditions, as this is crucial for the durability and safety of the structure.
What do DIN and ISO standards mean in the context of screws?
DIN (Deutsches Institut für Normung) and ISO (International Organization for Standardization) standards are key regulations that govern the production and quality of screws worldwide. DIN standards define detailed requirements for various types of screws, including their dimensions, materials, and strength classes. ISO standards, on the other hand, are widely used in international trade and cover many aspects related to product quality and safety.
For example, DIN 933 refers to hex head screws with metric threads. The strength classes in these standards are strictly defined, allowing for a uniform assessment of screw quality in various applications. The use of standards also facilitates the interchangeability of fasteners in different systems. Compliance with these standards is crucial to ensure that screws have the appropriate mechanical properties and fit the corresponding nuts.
In specific applications, it is important for engineers and designers to have access to strength class tables where they can check which materials will work best in their projects. These standards help ensure an appropriate level of safety and reliability, which is essential in industries such as construction, automotive, and aerospace. Thanks to DIN and ISO standards, engineers and designers can be confident that their choice of fasteners will comply with international standards, which impacts the quality and safety of their structures.