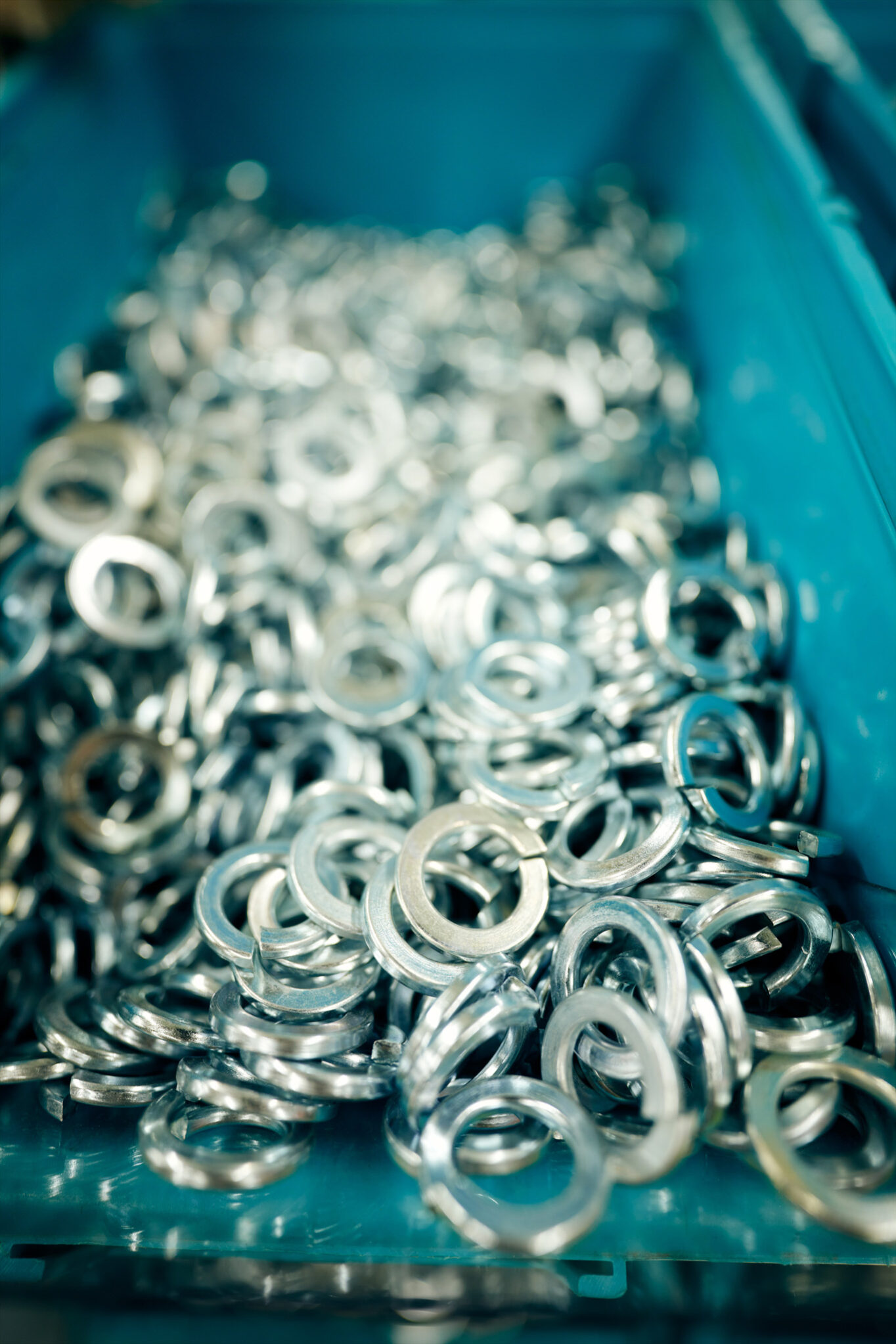
Washers for screws and nuts. Types and applications
Washers for screws and nuts play a crucial role in ensuring durable and solid screw connections. Thanks to the variety of washer types, they can be adapted to different applications and conditions, making them an essential element in many industries, such as construction and manufacturing. In this article, we will look at different types of washers, their purpose, and practical applications.
What are the types of washers for screws?
Types of washers for screws can be classified according to their function and the materials from which they are made. The most popular types are toothed washers, spring washers, and protective washers. Toothed washers, due to their design, provide better protection against loosening connections, which is important in cases of dynamic loads. Spring washers, on the other hand, work on the principle of tension, which prevents the nut from loosening due to vibrations. In addition to these types, there are also sealing washers, which serve as protection against fluid leakage.
It is also worth noting the leveling washers, which help stabilize screw connections, especially on uneven surfaces. When choosing the appropriate type of washers, it is important to consider the specifics of the application and mechanical requirements. Well-chosen washers for screws are crucial for the durability and safety of the entire structure, so they should be used in accordance with manufacturers’ recommendations and industry standards.
What is the purpose of washers for screws?
Washers for screws serve several important functions that significantly affect the quality of screw connections. The main task of washers is to distribute the pressure exerted by the screw head over a larger surface, which prevents damage to the material and increases the durability of the connection. Additionally, washers protect against loosening of nuts, which is particularly important in structures exposed to vibrations or variable loads. Properly selected washers can also protect against corrosion, which extends the life of the entire structure.
In the context of various applications, washers can be used in the assembly of mechanical devices, in construction, and in various industrial sectors. The use of washers in screw connections is crucial to ensure their stability and safety. Their proper use can also prevent the occurrence of looseness, which in the long term translates into a lower risk of failures and damage to structures.
How to use washers for screws and nuts?
Using washers for screws and nuts requires following several important rules that ensure their effectiveness. First of all, washers should be selected appropriately for the type of screw and the material of the joined surface. Washers should be placed at the very end of the assembly, before tightening the nut, to ensure proper pressure distribution. It is also worth remembering that in the case of spring washers, their proper placement can significantly affect the durability of the screw connection.
It is important to check before assembly that the surfaces of the washers and screws are clean and free from contaminants, which can negatively affect the quality of the connection. Additionally, when using toothed washers, make sure that the teeth are properly fitted to the surface of the nut and screw to ensure maximum effectiveness of their action. Proper use of washers for screws and nuts is the key to obtaining solid fastenings that will be resistant to various loads and operating conditions.
What are the differences between toothed and spring washers?
Toothed and spring washers have different applications and properties that influence their selection in specific situations. Toothed washers, due to their design, have the ability to “stop” the nut, which prevents the connection from loosening as a result of vibrations. They are used where dynamic loads occur and when it is necessary to protect against self-loosening. Spring washers, on the other hand, work on the principle of elasticity, which allows them to absorb vibrations and shocks, making them ideal for applications where variable loads occur.
In practice, the choice between toothed and spring washers depends on the specifics of the assembly and the conditions in which they will be used. Toothed washers work great in fastenings requiring high stability, while spring washers are more effective in situations where vibration damping is key. Each of these types of washers serves a different function in the context of screw connections, so it’s worth carefully considering their application in a given project to ensure the durability and safety of the connections.
What materials are used to produce washers?
The material from which washers are made is crucial for their durability and application. The most commonly used materials are steel, brass, and various plastics such as polyamide or PVC. Steel washers are characterized by high resistance to loads and damage, which is why they are often used in industry and construction. Brass washers, on the other hand, are more resistant to corrosion, making them an ideal choice for applications in humid conditions.
Plastics, such as polyamide, are used in applications where weight reduction and resistance to chemicals are crucial. The choice of the right material depends on the specifics of the application and requirements regarding strength and resistance to external factors. It is also worth paying attention to hardened steel washers, which are characterized by even greater durability and resistance to mechanical damage. Well-chosen materials for the production of washers have a significant impact on the lifespan of screw connections.
What problems can occur without the use of washers?
Not using washers under screws and nuts can lead to a number of problems related to the durability and safety of connections. The main threat is the risk of nuts loosening, which can lead to failure of the entire structure. In the case of dynamic loads, the lack of washers can result in damage to the material, which leads to weakened screw connections. Additionally, the lack of appropriate washers can expose the connection to corrosion, especially in humid conditions, which translates into a shortened lifespan of the fastenings.
In situations where washers have not been used, there may also be uneven distribution of pressure, which leads to cracks or deformation of the joined materials. The consequences of not using washers can be not only costly but also dangerous, especially in structures subjected to high loads. Therefore, it is extremely important to always use appropriate washers for screws and nuts to ensure the solidity and safety of all screw connections in every application.
- Washers for screws and nuts. Types and applications - 3 April 2025
- Marcopol’s 40th anniversary Gala. A night to remember - 3 April 2025