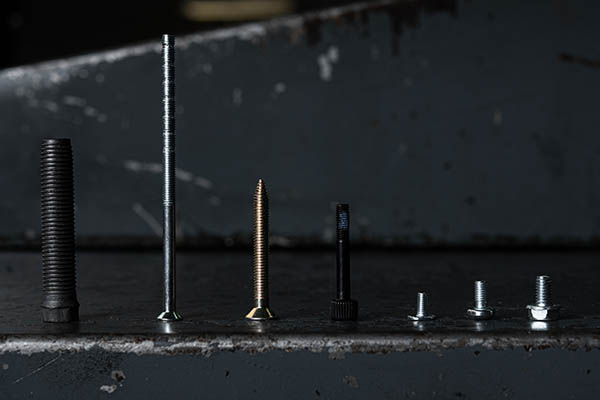
Why fastener quality is crucial in the production process?
In industrial manufacturing, every detail matters, and fasteners, such as screws, nuts, and washers, play a critical role in maintaining the integrity of structures. While they may not always be visible at first glance, the quality of fasteners directly impacts the safety, durability, and efficiency of the entire system. So why should you invest in high-quality fasteners? Let’s take a closer look at their importance in the production process.
Fastener quality and structural safety
The safety of any structure – from industrial machinery to buildings and vehicles – depends on the durability of its connections. Low-quality fasteners can lead to loosening, cracking, or corrosion, which can ultimately result in system failure. In industries where worker safety and machine reliability are paramount, fasteners that meet quality standards (such as ISO, DIN, or ASTM) ensure a higher level of safety and reduce the risk of failures.
Durability and cost impact
High-quality fasteners made from the right materials and adhering to strict durability standards ensure long-lasting connections, even in harsh conditions. Good resistance to mechanical loads, changing weather, or corrosion means less risk of premature failures. Investing in such components leads to longer-lasting structures, which translates into lower operating and maintenance costs. Avoiding cheap substitutes, which often fail at critical moments, is key to optimizing long-term expenses.
Production efficiency
In the design of production lines, every component must work flawlessly to ensure that the entire machine operates efficiently. Low-quality fasteners can cause production delays, machine breakdowns, and frequent repairs. High-quality fasteners are not only more reliable but also facilitate easier assembly, reducing production time. Ultimately, operational efficiency and production continuity are guaranteed when every fastener performs as expected.
Case studies: Failures caused by low-quality fasteners
There are numerous examples in history where low-quality fasteners led to disastrous system failures. In one case, faulty connections in the hydraulic system of a construction machine caused a sudden loss of pressure, leading to a work stoppage for several days, generating significant financial losses. In another instance, using fasteners with lower corrosion resistance in a bridge construction led to rapid deterioration, threatening the stability of the entire structure and requiring costly repairs.
In the aviation industry, where safety is the top priority, poor-quality fasteners can lead to catastrophic consequences. One well-known case involved loose screws in a critical engine component, which resulted in an emergency landing. As a result, industries such as aviation and automotive rigorously control fastener quality to prevent such incidents.
The quality of fasteners has a direct impact on the safety, durability, and efficiency of structures. Low-quality fasteners can lead to costly breakdowns, production delays, and dangerous situations. That’s why it is essential to choose products that meet the highest quality standards. Investing in high-quality fasteners is an investment in reliability and long-term system durability. At Marcopol, we understand the importance of quality, which is why we offer products that meet the highest standards, ensuring the safety and durability of your connections for years to come.