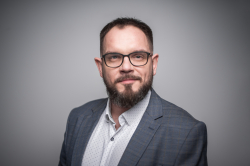
Tomasz Albecki Senior Product and Content Specialist
Senior Product and Content Specialist at Marcopol. Passionate about modern solutions in marketing and B2B product promotion. Privately, a father of two sons, fascinated by technology and market trends. On the Marcopol blog, he shares his knowledge and experience, bringing readers closer to the world of fasteners and industrial innovations.